Chemical fumigation treatment after 3D printed parts are printed is an important post-treatment process designed to improve the surface quality and performance of the printed parts, such as enhancing the surface quality, sterilizing, and removing residual materials, among many other functions. Its basic operation is as follows:
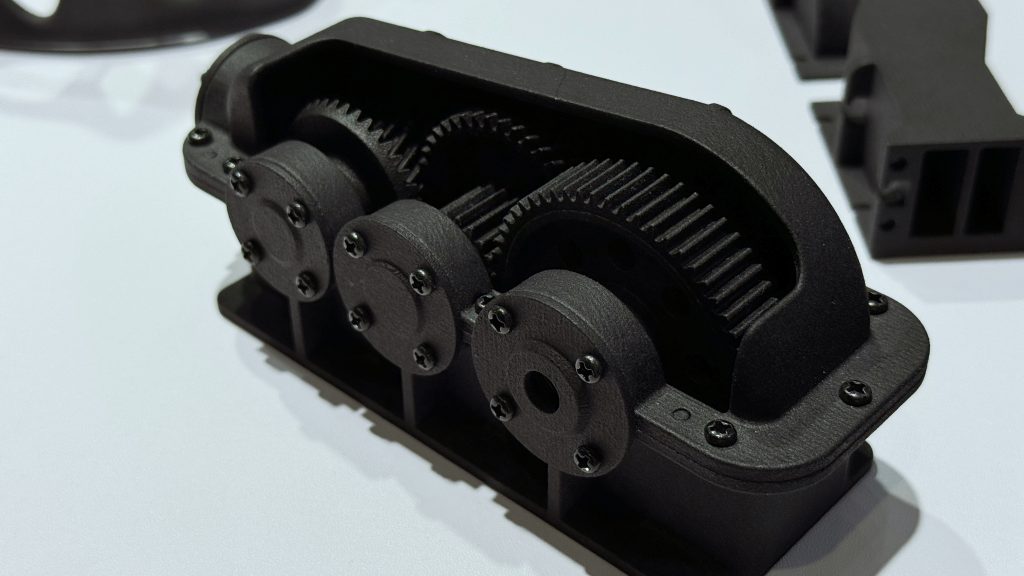
I. Preparation stage.
To be based on the desired effect of the part material and demand, carefully select the appropriate fumigant, such as for thermoplastics often choose acetylacetone and so on.
At the same time, ready for professional fumigation equipment, as well as operators need to wear protective gloves, goggles and gas masks.
Ⅱ. Parts pre-treatment
Overall drying or low temperature drying to prevent moisture interference with fumigation.
Ⅲ. Fumigation
Put the dried parts smoothly in the chemical steam polishing equipment, according to the material and size of the parts, as well as the characteristics of the fumigant, set the appropriate fumigation temperature and time.
Then start the fumigation equipment, so that the preparation of fumigant through the gas port slowly into the interior, at the set temperature evaporation, the formation of uniformly dispersed steam, fumigation of parts. During the fumigation process, the solvent vapor will have a chemical reaction with the surface of the parts, so that the microscopic bumps on the surface of the parts are preferentially dissolved, thus achieving the effect of polishing.
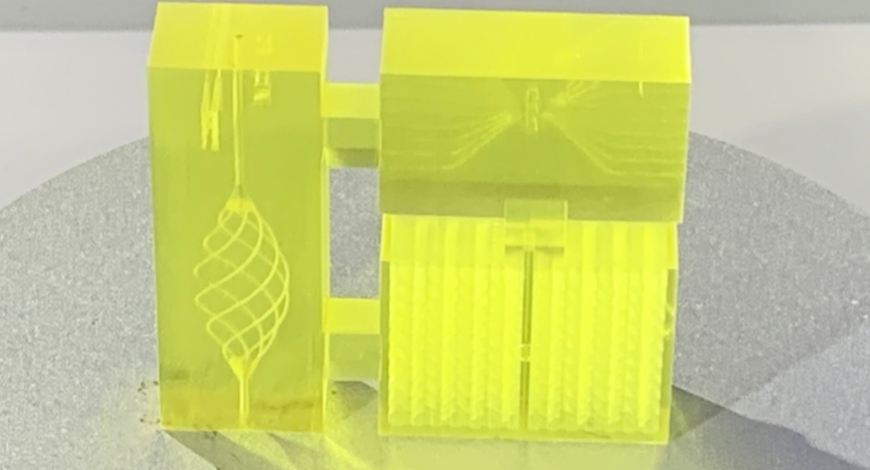
It is important to note that the fumigation process requires precise control of the time, ranging from a few hours to tens of hours, depending on the size and complexity of the part and the desired effect; in some cases, the pressure needs to be adjusted so that the air pressure inside the equipment is slightly higher than atmospheric pressure, which is usually done through the use of pressure regulating devices that maintain the pressure of the equipment in a safe range to ensure that the fumigant penetrates sufficiently to achieve the desired fumigant effect. This ensures that the fumigant penetrates sufficiently to achieve the desired fumigation effect.
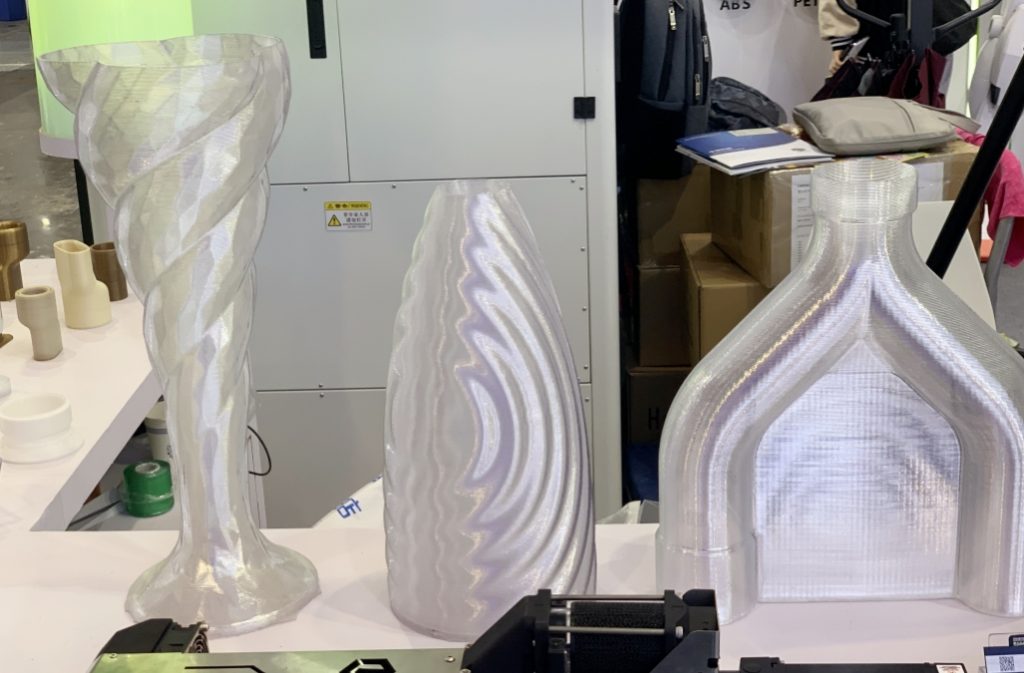
Ⅳ. Fumigation after treatment link
After the end of fumigation, you need to exhaust the fumigation equipment first. After ventilation, the equipment can be opened and the parts removed.
Then use the appropriate solvent to clean the fumigated parts to remove residual fumigant and reaction products.
The part is then dried to obtain the final fumigated 3D printed part.
Finally, the part needs to undergo a comprehensive quality inspection, such as surface hardness, abrasion resistance, dimensional accuracy and appearance, to ensure compliance with the requirements. If the inspection finds that the parts have quality problems, such as insufficient surface hardness, excessive dimensional deviation or defective appearance, the fumigation process parameters need to be analyzed and adjusted, and if necessary, the parts should be re-fumigated or scrapped to ensure that the quality of the final product meets the standards.
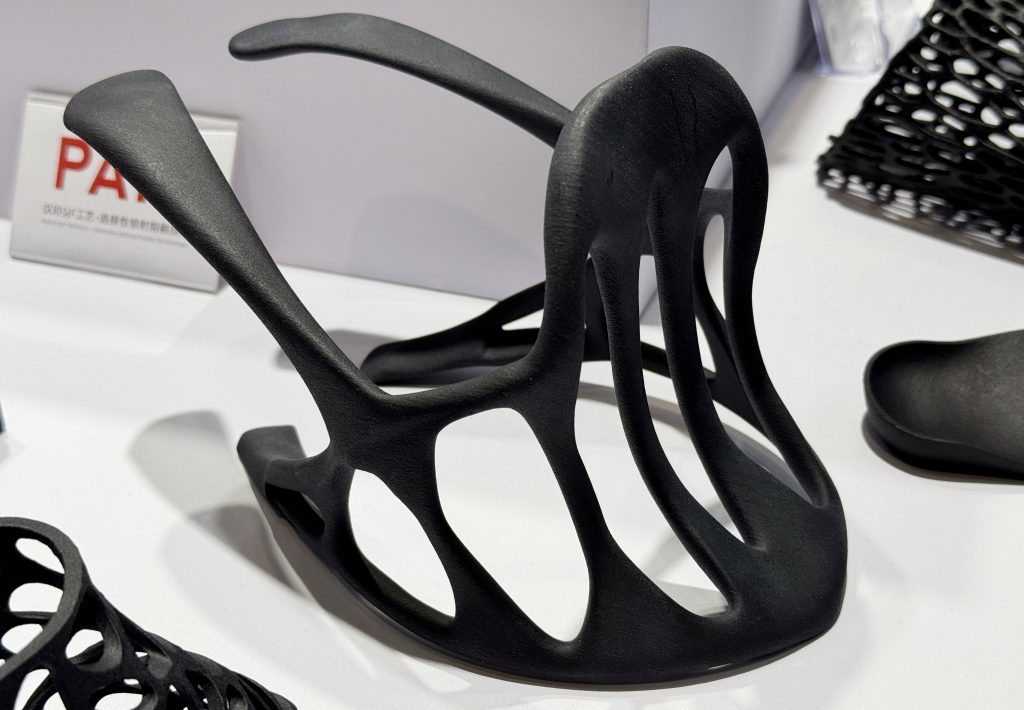
The fumigation process for 3D printed parts, undoubtedly, provides a powerful means for the optimization of 3D printed parts, which not only enhances the physical properties of the parts, but also improves their resistance to environmental and chemical corrosion, and has a broad application prospect in multiple fields. Moreover, with the continuous progress of technology, the fumigation process is also continuously optimized, and it is believed that the fumigation process will usher in more innovation and development opportunities in the near future.