With the development of 3D printing technology, research work will enter a new stage, and this is just a matter of time. “4D printing” is a recently defined category used to describe the integration of existing 3D printing technology and Mars material science to create a printed component whose configuration can be changed by environmental stimuli such as temperature and humidity. For these studies, this means that post-processing steps of mechanical programming need to be more closely integrated into the 3D printing process to save time and materials.
A team of researchers from Georgia Institute of Technology, Singapore Institute of Technology and Design (SUTD), and Xi’an Jiaotong University in China have recently developed a new 3D printing method to create objects that can permanently change their shape. Using Stratasys’ multi-material Objet 3D printer, the team laid layers of shape memory polymer, each layer designed to react differently when exposed to heat.
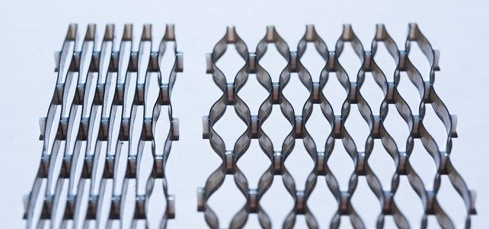
Smart shape memory polymer (SMP) is a material that “remembers” a shape and changes to another programmed shape when uniform heat is applied. For research purposes, the team created a model of a daisy with petals, which resembles a real flower exposed to the sun, and a lattice-like object that can expand eight times its original size.
Jay Jerry Qi, a professor at Georgia Institute of Technology’s George Woodruff School of Mechanical Engineering, said: “The new process will save important time and materials in the additive manufacturing process, while eliminating time-consuming mechanical design in design and manufacturing. High-resolution 3D printing Components can be simulated by computer, designed by 3D printing, and then directly and quickly converted into a new permanent configuration by simple heating.”
“Typical process requirements: 1) heat the polymer; 2) mechanically deform the polymer into a second shape; 3) lower the temperature; 4) eliminate external loads,” he said. “The polymer remains in a deformed shape (we call it a’programmed shape’). To recover, you only need to heat the polymer again, and the polymer will return to its original (permanent) shape. In our new method, just heat The printed structure (without mechanical deformation) will become a new shape.”
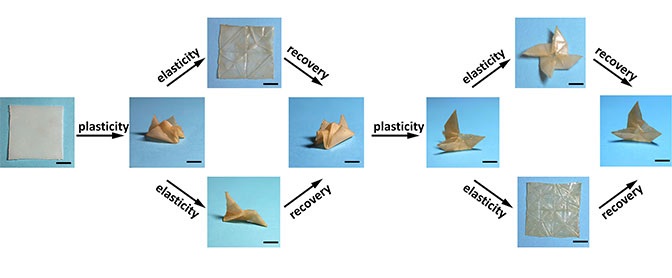
With the new process, the new shape remains stable and will not change when further heating or cooling. More interestingly, according to the team’s claim, this new material can have a shape memory effect, but it will take the new shape as its permanent shape.
The process of allowing high-resolution 3D repeatable programming structures will enable a variety of applications across fields, including aerospace, medical technology, and consumer products. It may even allow for new paradigms in product design, where components can be simultaneously designed to become multiple configurations during service.