In 3D printing, abrasive jetting is an important part polishing process that can significantly improve the surface quality of parts. The basic operation of abrasive jetting is as follows:
Ⅰ. Pre-preparation
(A) parts inspection
Before abrasive jetting, the surface condition of the 3D printed part must be carefully checked to ensure that the part has no obvious defects, and if there are defects, they need to be repaired or reprinted first to avoid further deterioration of defects caused by jetting. At the same time, it is necessary to clarify the size and shape of the part to provide a basis for subsequent operations.
(ii) abrasive selection
According to the part material and smoothness needs to pick the right abrasive. Like aluminum oxide abrasive hardness, suitable for grinding metal parts; silicon carbide abrasive cutting performance is good, commonly used in grinding composite materials or ceramic parts. The size of the abrasive particles is also very critical, general roughing with large particles (120 – 180 mesh), finishing with small particles (220 – 320 mesh).
(C) equipment installation and commissioning
Place the equipment in a well-ventilated place, connected to a stable source of compressed air, to ensure that the air pressure of the equipment is stable. Then install the abrasive supply device and load the abrasive into the supply container. Check whether the spray nozzle is installed correctly, generally there are 0.8 – 2.0mm apertures to choose from, for fine parts surface treatment, you can choose a smaller aperture of the spray nozzle. Commission the equipment to ensure that the abrasive is sprayed evenly.
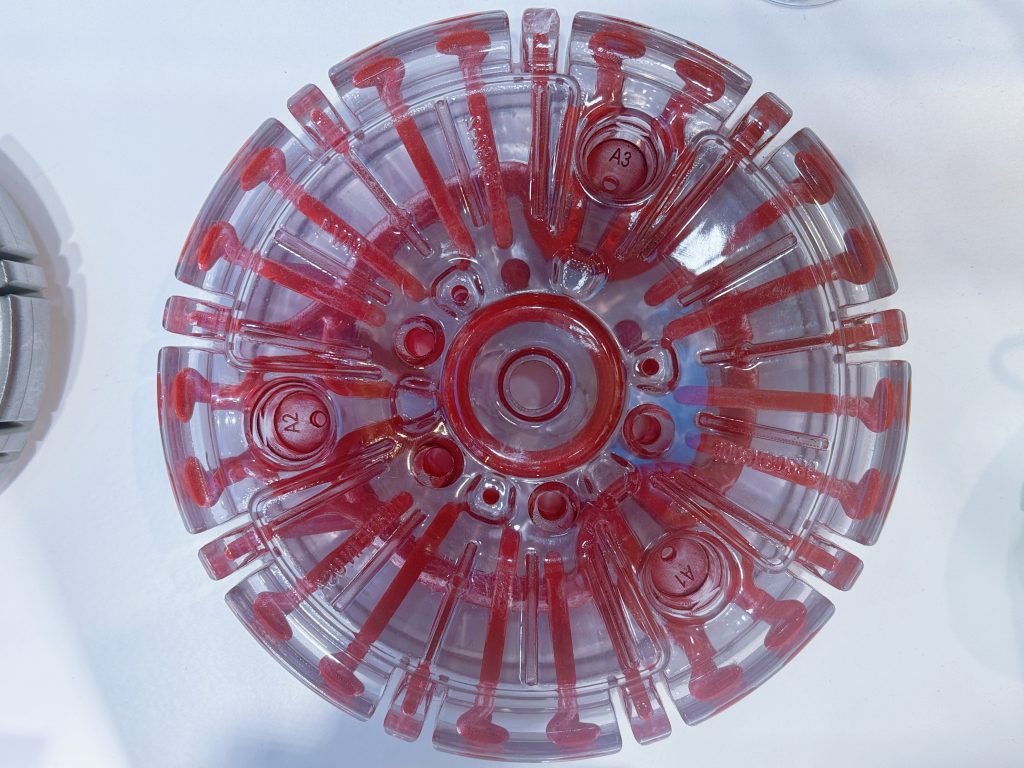
Ⅱ.The spraying operation process
(A) parts fixed
The parts will be firmly fixed in the workbench or special fixture, to prevent the abrasive jetting due to the impact of the abrasive flow and displacement, affecting the polishing effect, irregular parts can be customized fixture.
(ii) Parameter setting
According to the part design requirements set the spray parameters. Spray angle is generally selected from 30 to 90 degrees, 90 degrees for flat parts; spray distance is usually set at 10 to 50 cm, the initial can be set to 30 cm and adjusted according to the effect; spray time is based on the size of the part and the surface roughness to determine the first short test, and then gradually adjusted.
(iii) Formal spraying
After the operator puts on the protective equipment, turn on the equipment and spray according to the set parameters. Keep the nozzle and the relative position of the surface of the parts is stable, so that the abrasive uniformly cover the surface to be polished, can be used in zoning spray method.
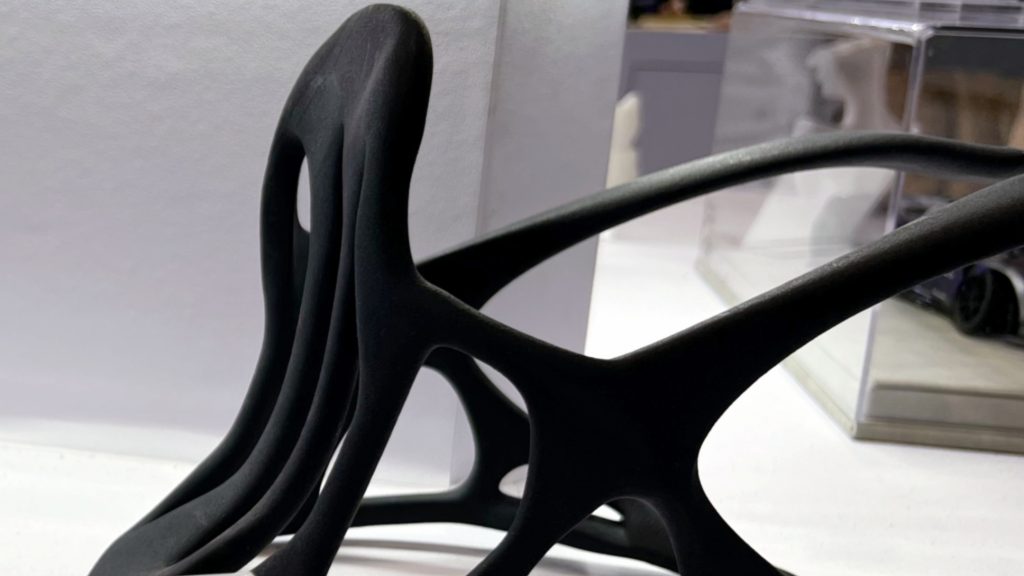
Ⅲ. Post-processing
(A) parts cleaning
After the completion of spraying, compressed air guns, brushes or ultrasonic cleaning machine can be used to remove residues on the surface of the parts. Complex shaped parts can be immersed in a cleaning solution (such as alcohol) for 10 – 30 minutes, and then rinse with water, compressed air blow dry.
(ii) Quality Inspection
Check whether the surface of the parts up to standard, the surface roughness meter can be used to measure and compare with the design requirements, if it does not meet the standard can be sprayed again or use other processes to supplement. At the same time check whether the size of the parts change, if out of tolerance, it is necessary to repair or re-processing.
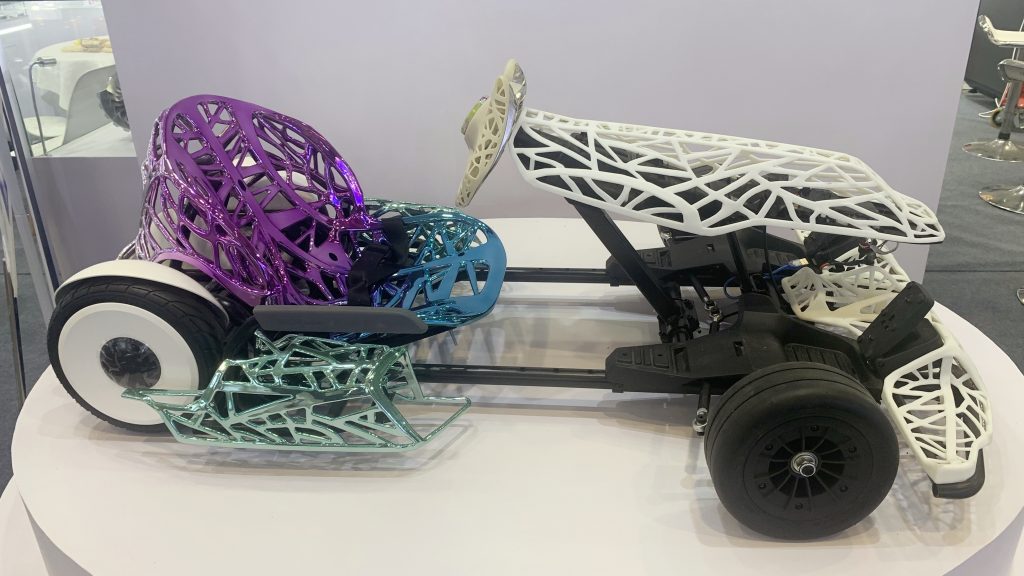
So far, 3D printing parts polishing process of abrasive spraying of the basic operation is completed, through the strict abrasive spraying operation process, can ensure that the surface quality of the parts to meet the design requirements, to meet the needs of practical applications.