CNC Machining Materials
Metal materials commonly used in CNC machining
When selecting materials for parts or products, many factors should be considered, including machinability, price, corrosion resistance, strength, weight and appearance. CNC machining is one of the most common manufacturing methods used to manufacture parts and products. The most common materials used for CNC are as follows:
Al6061 – It is the most common general aluminum alloy brand. It is usually used for automobile parts, bicycle frames, sporting goods, remote-control vehicle frames, etc. similar to other aluminum alloys, it has a good strength to weight ratio, atmospheric corrosion resistance, and good processability. When exposed to brine or other chemicals, it also has poor performance, depending on the use of the product.

Al7075 – It is one of the strongest aluminum alloys with general machinability. This material is an ideal choice for high-strength entertainment equipment, automotive and aerospace frames. These applications require metals to withstand conventional stresses, and should be avoided when welding is required.
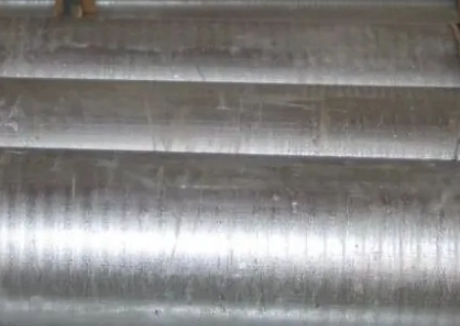
Brass – Brass is common in pipe fittings, home decoration and musical instruments, mainly because of its soft material and easy processing. Brass has high polishing property.
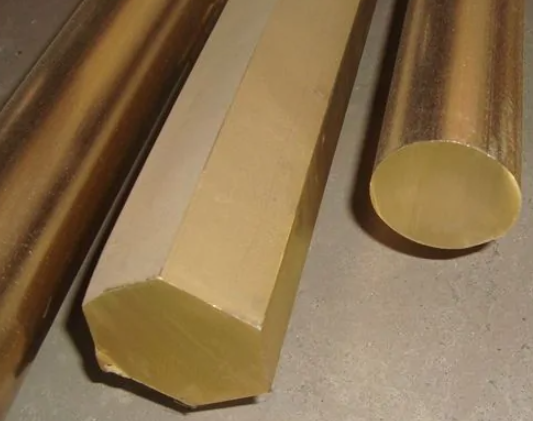
Mgaz31 – A magnesium alloy that is 35% lighter than aluminum with the same strength. This material is usually more expensive and is usually used for aircraft components. This material is easy to process, but it has flammable characteristics. Its light weight and high strength are often used for notebook computer housings, power tools, camera bodies and other uses around houses.
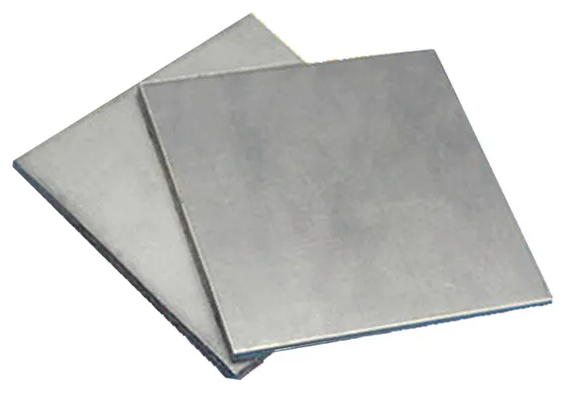
SUS304 – The most common stainless steel. SUS304 is very tough, non-magnetic, easy to process and generally corrosion resistant, making it an ideal choice for kitchen accessories, water tanks and pipes used in industry, construction and automobiles. It exists in a variety of consumer and industrial parts and products.
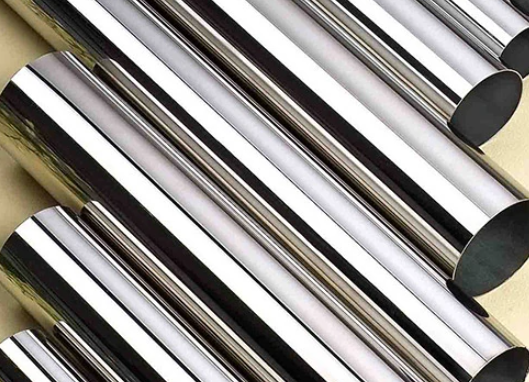
SUS316 – A stainless steel, tough and easy to weld, is very corrosion-resistant, and is ideal for construction, marine accessories, industrial pipes and automotive applications.
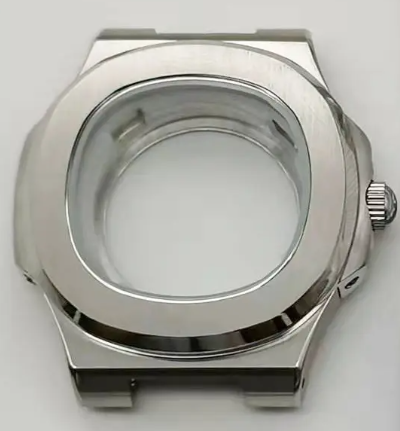
SUS430 – A stainless steel with strong magnetism, which can be used in applications requiring rust prevention and magnetism absorption.
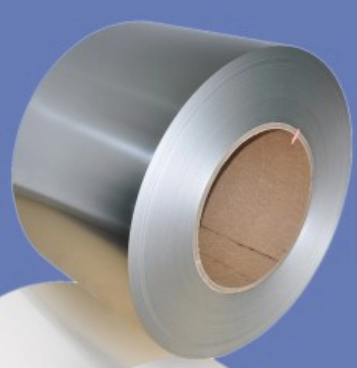
Carbon steel 1045 – This strong and tough material is a low carbon steel, usually cheaper than stainless steel, which can be hardened and heat treated to make it easy to process and weld. It is most commonly used in industrial applications and mechanical parts requiring high toughness and strength, such as nuts and bolts, gears, shafts and connecting rods.
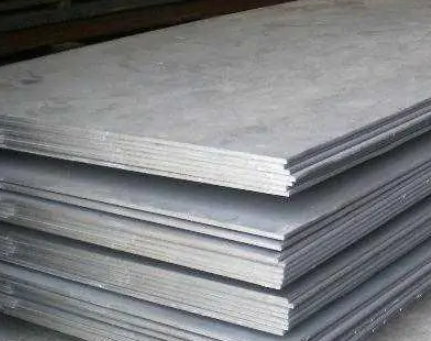
Ti – Titanium alloy, characterized by high strength, light weight and toughness. Titanium alloys can be easily welded and anodized to provide protection and appearance. It is a good conductor of heat, but its polishing effect is poor and it is a poor conductor of electricity. And it is usually more expensive than other metals.
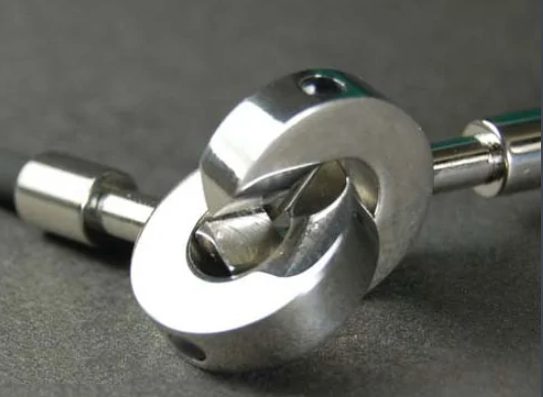
The most commonly used materials for designing CNC processing products are listed above, and there are more to choose from. In order to ensure the most accurate and efficient materials are selected, suggest to work closely with relevant material manufacturers.